They move silently through production halls, transporting goods and materials to exactly where they are needed: auto-guided transport systems. The Pepperl+Fuchs plant in Trutnov (Czechia) has also been using driverless transport systems since the beginning of the year.
Long walking distances and waiting times were previously the order of the day for employees at the Czech Pepperl+Fuchs plant. “There was only one elevator in the entire building for handling the entire flow of materials and for transporting raw material from the ground floor to the upper floor on a trolley,” recalls Lean Consultant Stepan Potocek. When it was eventually certain that a new building would be constructed in Trutnov, the Lean Consultant’s team had its hands full with optimizing future production processes and logistics from the ground up, saving avoidable walking distances and therefore a lot of time – entirely in line with the Lean Management concept.
After a one-year construction phase, in the middle of 2020 the point was reached when the plant had been relocated to a completely ground-level facility with a production area of 3,000 m², a warehouse of 1,500 m², and 1,500 m² of technical facilities.
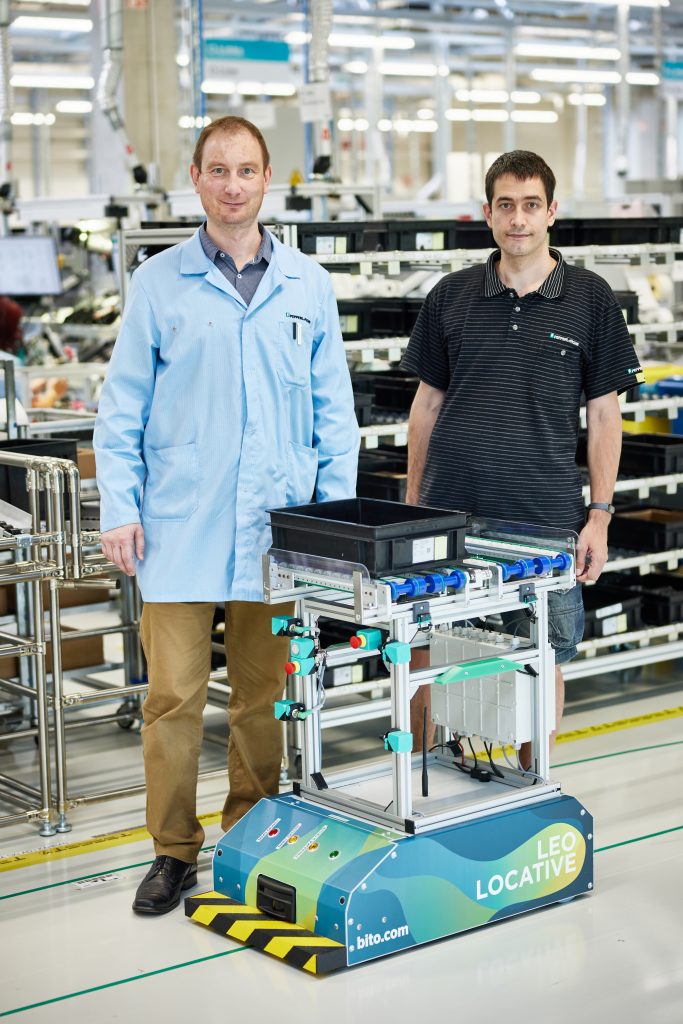
are pleased with the new
production assistants in Trutnov.
“Five months before, we had already formed an in-house team of six people who focused on needs analysis and the creation of a new plant design,” says Potocek, reflecting on the initial planning phase. The result was a completely revised production concept according to which practically all manufacturing cells are arranged in a U-shape, each with their own transfer points for raw material, Kanban material, and finished products. Since these special stations are located directly on the main transport route, a basis was also created for using automated guided vehicles (AGVs).
A well-thought-out goods cycle
Furthermore, the newly constructed building features two roll-up doors which connect production with the warehouse. “In this way, finished goods and empty Kanban boxes can easily be transported on driverless transport systems through one door and material that is still to be processed through the other door, which is located in the middle of the production hall,” he adds. This creates a well-thought-out goods cycle which enables automated RFID-based monitoring of incoming and outgoing Kanban material. The basis for the new concept and therefore also the search for a suitable auto-guided transport system solution was the value stream map, which the team had already created during the initial planning phase. This map depicted the future flow of goods and showed the resulting requirements and needs in order to design the production processes.
No collisions
Before the driverless transport systems could be incorporated into the production process, a number of different design and functionality requirements had to be taken into account. For example, the AGVs were equipped with the R2000 2-D-LiDAR sensor by Pepperl+Fuchs to ensure reliable detection of the surroundings and to avoid collisions. “Our PGV DataMatrix positioning system is used for the optical tracking of driverless transport vehicles,” explains Pavel Grund, who accompanied the rollout as EMS Test Support Engineer from the very beginning. This consists of a camera system with an integrated lighting unit, which reliably detects color tapes and DataMatrix code tapes attached to the floor, even in tight bends. The diffuse mode sensor, in turn, monitors the loading operation and sends a start signal to the AGV to move on to the next stop.
But that’s not all: The system has been expanded with additional components as well as an RFID system. These components include an inductive sensor, which reliably detects whether the vehicle is inside or outside the transfer station. Once there, the retroreflective sensor with integrated background suppression monitors the loading operation and detects whether the boxes have been correctly positioned so that they do not fall off during further transport.
An RFID read/write head and an IDENTControl interface are attached to each side of the two roll-up doors. The transport vehicle has an RFID tag which triggers the roll-up door to open as soon as it approaches. Kanban boxes are also equipped with RFID tags so that material flows can be monitored at all times.
More protection for people and material
The Czech team was therefore able to develop an intelligent intralogistics concept, making long journeys and searching for materials a thing of the past. Potocek sums it up: “Thanks to the LEO Locative transport system and the perfectly matched sensor technology, we not only save time, but also reduce the risk of accidents many times over so that neither people nor materials come to any harm.”
Read more about the use of AGVs at the P+F site in Trutnov in Amplify.